Kemxx Nigeria limited have over the years of operation worked and developed on IMPP system to protect the onshore/offshore pipeline against corrosion and extreme temperatures to prevent cold spots, cracks and failures
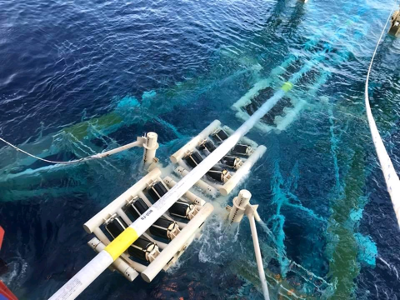
FIELD JOINT COATINGS
The field joint is the bare steel area where two pipe sections meet and are welded together. Offshore pipelines and subsea production structures have thousands of field joints that need protection against corrosion and extreme weather. Quality field joint coating systems not only protect against corrosion prone areas and cold spots but also offer the following:
- Long-term anti-corrosion and thermal insulation performance
- Excellent bonding to the steel substrate
- Compatibility with the parent coating system applied on the pipe joints
- Easy application and installation in any conditions and locations
- Short application and installation cycle time
INJECTION MOLDED POLYURETHANE (IMPU):
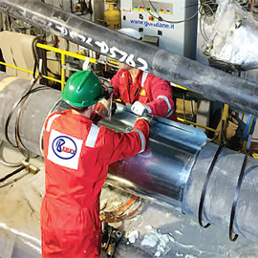
Kemxx’s specializes in multi-layer anticorrosion systems, designed and application in a wide range of thicknesses and layers to meet insulation and subsea installation requirements. Linepipe coating is applied by side extrusion and is completed by the KEMXX advanced PP Injection Molding technology for field joints.
This world-class, reliable technology provides integral protection and an excellent interface between the parent linepipe coating and the field joint infill, and is suitable for reeling, J-lay and S-lay installation.
INJECTION MOLDING
Field joint coating services involve the coating of the girth welds produced on board the pipe-laying vessels or at any offshore location. KEMXX carries out the engineering, design and fabrication of customized field joint coating equipment.
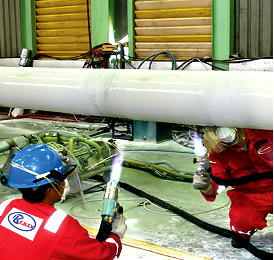
LAME SPRAYED POLYETHYLENE/POLYPROPYLENE (FSPE/FSPP):
In order to provide a totally compatible field joint coating system for 3-layer polypropylene- or polyethylene-coated pipelines, KEMXX has refined the process of applying PP or PE powder through the flame spray technique.
Excepteur sint occaecat cupidatat non proident.
Powder is carried in a stream of air and is fed into the center of an annular combustion flame where it is heated.
A second outer annular nozzle feeds a stream of air, around the powder stream, which accelerates the spray particles toward the substrate and prevents burning of the powder.
The system uses existing equipment for abrasive blasting/surface preparation and application of Fusion Bonded Epoxy (FBE) plus chemically modified polypropylene or polyethylene (CMPP or CMPE) dual-powder base layers. The overall thickness required is then achieved by applying powder with a flame spray gun.
The flame spray field joint coating system provides a full 3-layer system, which is highly adjustable to field conditions where coating thicknesses of up to 5mm are required.
The flame spray system can also provide a useful service for tie-ins or serve as a backup for a polypropylene or polyethylene Fused Field Joint (FFJ) system as well as being a thoroughbred field joint coating system in itself.
KEMXX’s polypropylene flame spray system has an extensive track record of use on onshore and offshore pipelines, as well as in spoolbases.
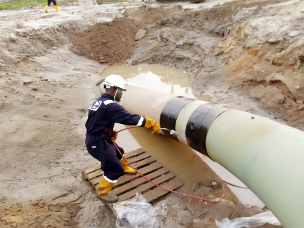
HEAT SHRINKABLE SLEEVE (HSS):
Corrosion protection in offshore and onshore applications with a variety of products. CORROSION PROTECTION HEAT-SHRINKABLE SLEEVES IN ANY LOCATION YOU REQUIRE
For more than 5 years, KEMXX has been a leading specialist of specialty pipeline coatings for the sealing and corrosion protection of pipeline joints and other substrates. We can provide our heat-shrinkable sleeve systems offshore on pipelaying vessels or onshore on spoolbases and in any other locations needed.
FUSION BONDED EPOXY (FBE):
KEMXX has developed a range of service solutions for the efficient application of powder-applied coatings to the welded field joint area, supported by many years of experience.
Fusion Bonded Epoxy (FBE) powder coatings are applied to the welded joint area as a standalone coating system for FBE-coated pipelines or as a primer layer as part of multi-layer polyolefin field joint coating systems for multi-layer polyolefin-coated pipelines.
FBE application solutions and services to welded field joints include:
Semi-automated powder application equipment and services
Fully automated, combined heat-and-coat, powder application equipment and services
Key FBE Features
- Controlled thickness
- Efficient application cycle times
- Reduced waste and hazards to the environment
KEMXX strives to meet the highest levels of quality while maintaining the highest levels of productivity in the firing line. Our specialist technicians are trained in all disciplines and the operation of KEMXX application equipment.
FBE Application
The application of FBE powder coatings involves pre-heating the substrate to the required temperature (typically 240°C) by use of induction coils, followed by application of the powder coating.
KEMXX offers powder coating application services.
Semi-Automated Powder Application Equipment and Services
KEMXX has many years of experience in the application of powder coatings, using our semi-automated equipment and processes in the firing line. Our semi-automatic powder application equipment is available for a wide range of pipeline diameters.
KEMXX’s semi-automated powder coating equipment rotates around the field joint area in cycles to achieve the desired dry film thickness (DFT). These units are also used for the application of FBE and polyolefin adhesive as part of multi-layer systems (the FBE and polyolefin adhesive are interlocked together).
Fully Automated Powder Application Equipment and Services
In response to the industry, for optimum cycle times and high repeatability, KEMXX developed the RAPTOR heat-and-coat machine.
RAPTOR units are fully automated, designed to simultaneously pre-heat and apply powder coatings to the field joint area in high-production environments such as spoolbase operations, multi-jointing activities, offshore lay barges, and onshore pipeline construction.
The units are fully contained, offering the highest levels of HSE protection to the environment and operator. RAPTOR units are also used for the application of FBE and polyolefin adhesive as part of multi-layer systems (the FBE and polyolefin adhesive are interlocked together).
THERMALLY SPRAYED ALUMINIUM (TSA):
- Thermal sprayed aluminium (TSA) coatings are widely specified for the protection of steels from aqueous corrosion in seawater environment e.g. offshore structures, risers, pipe components and ship structures.
- The main service conditions for the application of TSA include seawater immersion, tidal and splash zone and marine atmosphere.
- The successful use of TSA coatings in offshore applications such as tension leg elements and production risers in deep seawater have been reported in the literature.
- Toughness, low maintenance requirements, and long-term service life are among the desirable properties offered by TSA coatings for offshore applications.
- The basic properties of a TSA coating for long-term service are its barrier characteristics combined with good adhesion and an ability to provide cathodic protection to exposed steel. It was reported that a 200µm thickness TSA coating would provide a service life in excess of 30 years in a splash zone environment if optimised.
- Key factors for optimisation include TSA alloy composition; surface preparation; choice and application of a sealer; service application; electrochemical/galvanic exposure conditions; coating application techniques and process parameters. The stringent requirement of the offshore industries (e.g. oil and gas) to have a maintenance free coating system, with an expectation of up to 50 years life in severe environments, has increased interest in TSA coatings viable economic alternative to paint based systems.
- Although it has been demonstrated that TSA deposited by conventional spray systems can work well over extended periods, incidents of premature coating failure due to blistering and detachment have been recorded, indicating that coating quality and coating application procedure is extremely important.
- Porosity, oxide content and non-uniformity in the TSA coatings produced by the conventional systems are believed to result in reduced corrosion protection and shorter lifetime. Recent developments in spraying equipment via modification in nozzle and gun design, and process parameters (such as higher gas flow rates and gas pressures) are believed to produce TSA coatings with improved properties.
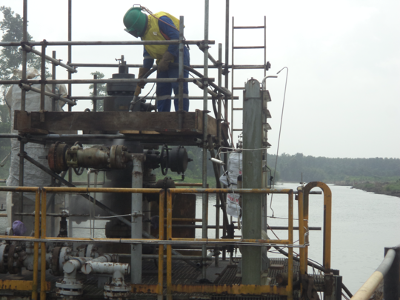
BLASTING AND COATING
KEMXX is familiar with several variations of wet abrasive methods, however the two most commonly used ones are highlighted below:
- Hydro-blast process: Sand is mixed with water and propelled by water pressure
- Vapour-blast process: The abrasive is suspended in a liquid projected at high velocity by a forceful flow of compressed air
Benefits of Wet Abrasive Blasting
Key benefits of wet abrasive blasting are listed below:
- Extremely fine media can be used
- Media impregnation into substrate is not possible
- Deeply cleans irregular surfaces
- Eliminates the need for hand-sanding
- Eliminates the need to use toxic chemicals
- Reduces dust
- Closed cabinet recycles media/slurry
- No heat warping with thin parts
- Final finish is appealing with a satin feel
- Provides an excellent surface for plating
- Provides an excellent surface for bonding
- Holds tight tolerances
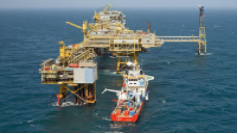
ONSHORE/OFFSHORE FACILITY MAINTENANCE:
KEMXX NIGERIA LIMITED is solely a corrosion control servicing company with a track record on various corrosion prevention and cathodic protection engineering and technical services. This has been achieved by taking special care in bringing resources with appropriate materials and skills for required projects together to meet our client’s goal.
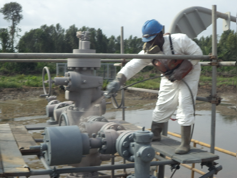
WELL HEAD/XMAS TREE MAINTENANCE:
KEMXX NIGERIA LIMITED has the technical capacity to design and apply protective coating that will best suit client service environment. We consider the terrain, the temperature, the chemical and the factors that could speed up the rate of corrosion ranging from the conductor casing, conductor pipe, lower master valve, casing spool, well head and xmass tree. This has been achieved by taking special care in bringing resources with appropriate materials and skills for required projects together to meet our client’s goal.
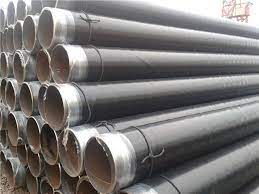
LINE PIPE COATING DIVISION:
KEMXX NIGERIA LIMITED has a department that designs and execute shot blasting, steel pipe interior coating, FBE/3LE/PP/PE Coating, steel pipe concrete weight coatings (CWC), steel pipe foaming for onshore/offshore installation.
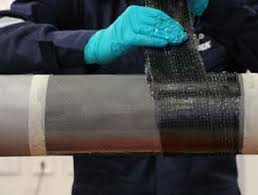
COMPOSITE WRAP FOR PIPE LINE REINFORCEMENT
Composite repair systems using composite wrap remain a constant repair option for industries requiring the repair and rehabilitation of piping systems. Various techniques and testing methods, which have the ability to handle different critical conditions onsite, are being developed in order to meet the demands of the industry. Composite wrap materials are recognized as a reliable and effective means of repairing corrosion damage, mitigating corrosion concerns and keeping critical piping systems in production.
Benefit of Composite Repair for Pipe and Tank Leaks Using Composite Wrap:
- Customized solution for through wall defects for pipes and tank walls
- Compliant installed by trained and certified applicators
- Engineering Calculation Report and Method of Statement for each repair
- ISO24817 and ASME PCC2 standards
- Provide excellent strength, bonding and chemical resistance
- Safes cost/time
Benefit of Composite Repair for Pipeline Reinforcement Using Composite Wrap:
- Customized solution for thin wall defects for pipes and tank walls
- Compliant installed by trained and certified applicators
- Suitable for wall loss up to 80%
- Engineering Calculation Report and Method of Statement for each repair
- ISO24817 and ASME PCC2 standards
- Provide excellent strength, corrosion and chemical resistance
- Safes cost/time
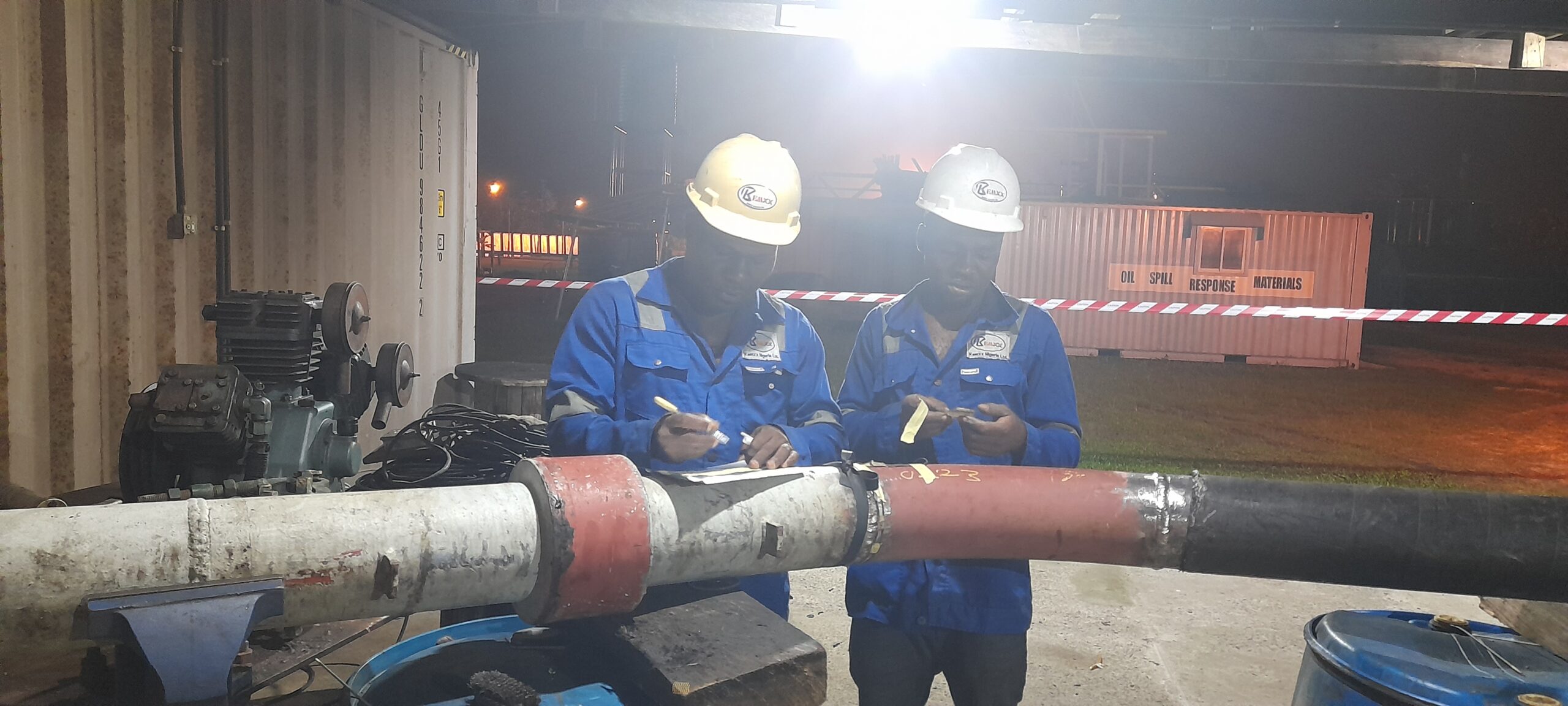
PIPELINE CORROSION INSPECTION DIVISION:
Metal loss is a critical pipeline threat. The integrity of your pipeline plays a critical role in the overall success of your business. Anomalies such as corrosion and gouging can cause metal loss, significantly reducing pipe wall thickness. Against this background, measuring this key parameter and determining the safe operating pressure are of the utmost important
KEMXX NIGERIA LIMITED offers high-resolution pinhole and pitting metal loss inspection service and standard.
The high-resolution pinhole and pitting service reliably detects defects and size as small as 5mm (0.2 in) diameter, which represents a two-fold improvement in the minimum sizing threshold, from the previous entry level ultrasonic service of 10mm (0.4 in).
At the onset of each project, we identify your unique requirements and tailor our service accordingly. Moreover, you can be sure of especially high-standards of reliability, expertise and responsiveness.
Our global engineering department has the skills and experience to efficiently manage complex and multi-diameter, deep-water and bi-directional inspections. For metal loss inspection, we have developed a comprehensive range of proven robots, incorporating ultrasonic technologies.
BENEFITS
- Circumferential resolution 4mm (0.2 in)
- Minimal axial resolution 0.75 mm (0.03 in)
- Metal loss inspection, quantitative wall thickness measurement with pitting resolution
- Provides the best resolution for the pitting detection and sizing
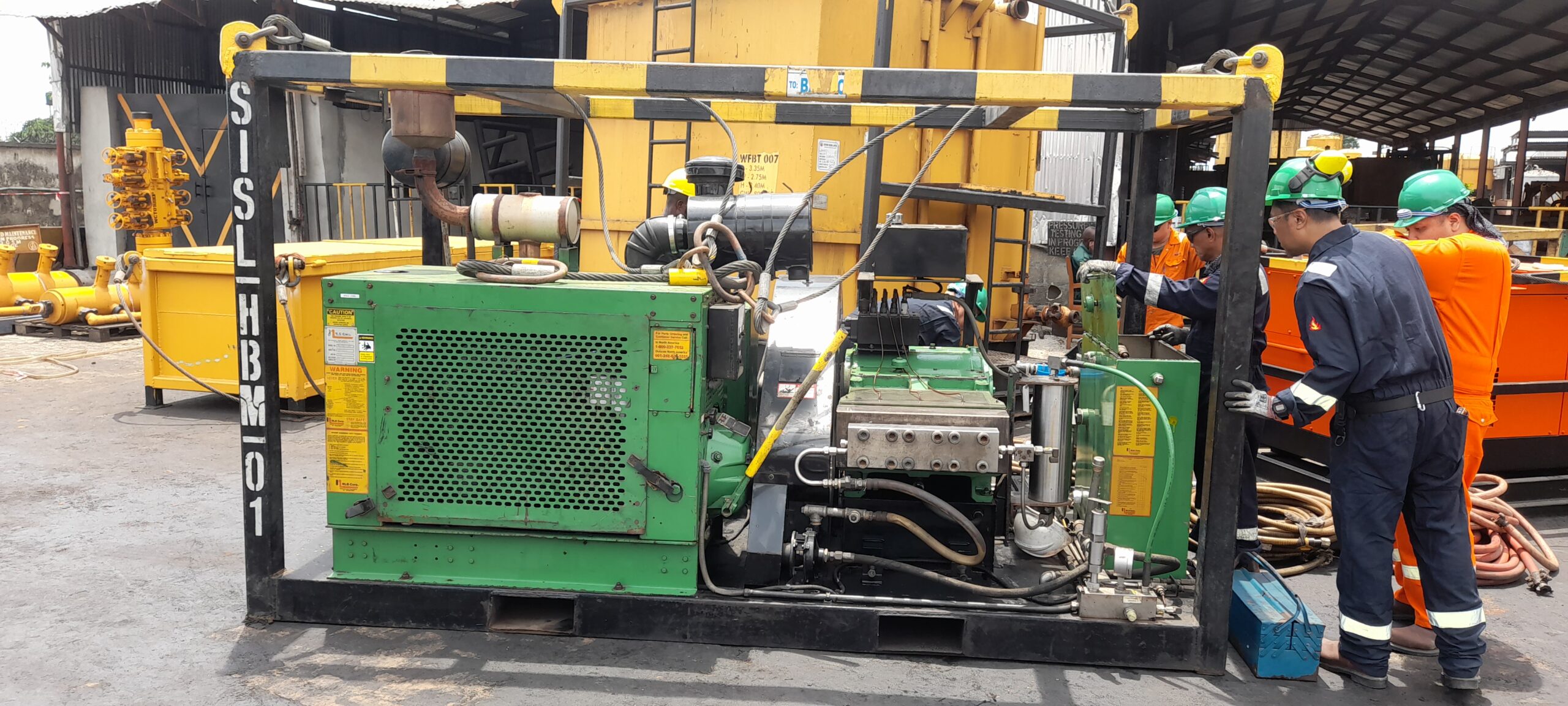
ULTRA-HIGH PRESSURE HYDROBLASTING & CUTTING:
- Our highly customized and automated systems utilize water pressure up to 40,000 psi for safe effective cleaning, surface preparation and cutting.
Benefits of Ultra-High Pressure Hydroblasting
- The dynamics of high-speed, pulsating water from ultra-high pressure hydroblasting produce incredible benefits for industrial cleaning, surface preparation, and cutting applications. The energy generated by the UHP water jet exceeds the bonding energy of even the most adherent scales, coatings, or process contamination.
Reduce Your Downtime
- Specially designed equipment, automated tooling, and a vast number of different nozzle configurations increase the ways you benefit. UHP water blasting reduces downtime, and improves safety performance.
- You will get the ultimate in reduced downtime and improved safety and precision. We engineer a custom job design with experienced employees and specialty automated equipment.
- We also provide the responsiveness you need with minimized travel time. Our teams and equipment are highly mobile and available throughout our vast geographical service area.
FIRE PROOFING
Intumescent coatings can offer 120 minutes maximum of fire protection to structural steelwork. At normal temperatures it looks like paint (it is nowadays even available in a glossy finish). When the temperature strongly increases due to fire, then the foam – like coating insulates the steelwork from the high temperatures.